TECHNOLOGY
See the unique way of multipowder production. In respect to potential risks of explosion, we really make sure that the entire production technology is safe.
Description of our technology
Safety first
We consider the safety of the entire production technology of the utmost importance. We put high importance on safety of our technology. The mill room is safeguarded against explosions, using anti-explosion structural features (relief flaps, break-through membranes, vacuum interruptors), and through inertization of CO2, used also in purification processes in silos. We use several active elements of inertization that have sensors throughout the entire system. Monitoring or, if need be, an activation of the emergency safety systems, happens when acceptable temperature and pressure levels are exceeded, or, when source of light coming from an explosion is detected. Our technology is equipped with HRD system, which is able to detect such explosions and suppress the impact of pressure to a minimum at its very onset. The risks associated with glow, ignition, or, as the case may be, explosion, are minimized through active monitoring of CO2 levels in the system.
The entire technology, including conveyor belts, is roofed. This enables all year-round production at very stable conditions. In turn, that has a positive influence on continuity of production and milling process stability, along with a good quality of the end product. Pendular mill combines high effectivity of milling with process stability.
Examples of our technology:




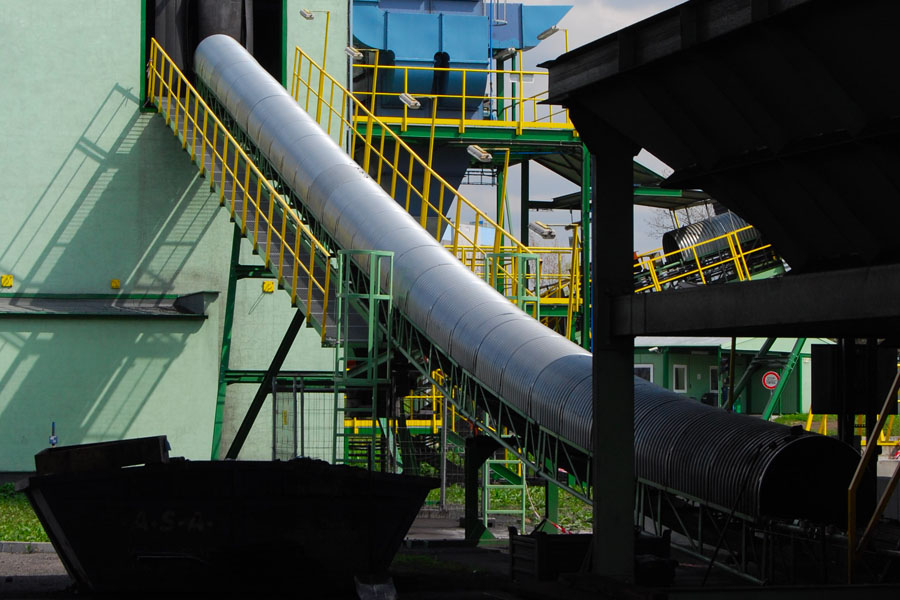





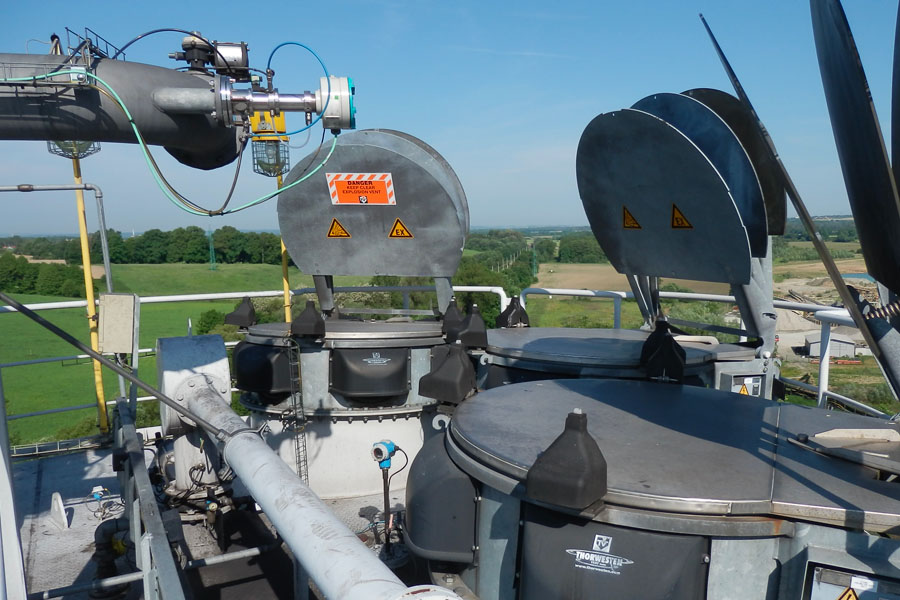
The milling processes
Raw material is stored at a 5,000-ton capacity storage facility or, alternatively, at an outside 30,000-ton capacity stock yard. Then, using conveyor belts, it is transported to a sorter, where we are able to sort out pieces in 2 different fractions. The undersize is subject to milling and drying
The milling process is set up to 40 tons an hour, depending on the incoming material. The annual production capacity of our plant is 180,000 tons. Multipowder is stored in two 500 m3 capacity silos, and, in a set of rail tank cars. This enables the distribution of several different types of multipowder at the same time. These materials are then loaded into rail cars or tank trucks according to customer’s specifications.
Milled black coal and biomass multipowder are transported in the ADR/RID mode. Multipowders of inorganic origin, like EKO ASH 450, typically designed for cement or batch plants, are transported in a regular mode.

Quality
Multipowder continuously undergoes quality monitoring during the milling and drying process from input to output, which ensures high quality monitoring. This allows us to adapt the milling process parametres to an input analysis. These in-between operational checks are carried out continuously throughout the process of production. Before being shipped, the resulting parameters of the output materials are determined by independent, accredited labs, and delivered to customers according to their specifications. The aim of quality control is to maximize efforts to ensure both output stability parameters, and thereby also achieving process stability with our customers.