Hard coal and antracitic multipowders
What is hard coal multipowder?
Hard coal multipowder is highly refined, fine-grained fuel, with highly active surface.
It is characterized by great ignition properties, reactivity, and excellent combustion behavior. Multipowder excells at great ability of flowing and fluidization that ensures comfortable usage, similar to that of liquid or gaseous fuels. Hard coal multipowder is a state-of-the-art energy source for furnaces and process combustion units. Its undeniable advantage is energy cost-cutting, at minimum investment and, often, the possibility to use your current equipment. The uses of our multipowders are many, and handling is not complicated. It is transported in the “dangerous substance” mode, according to ADR/RID.
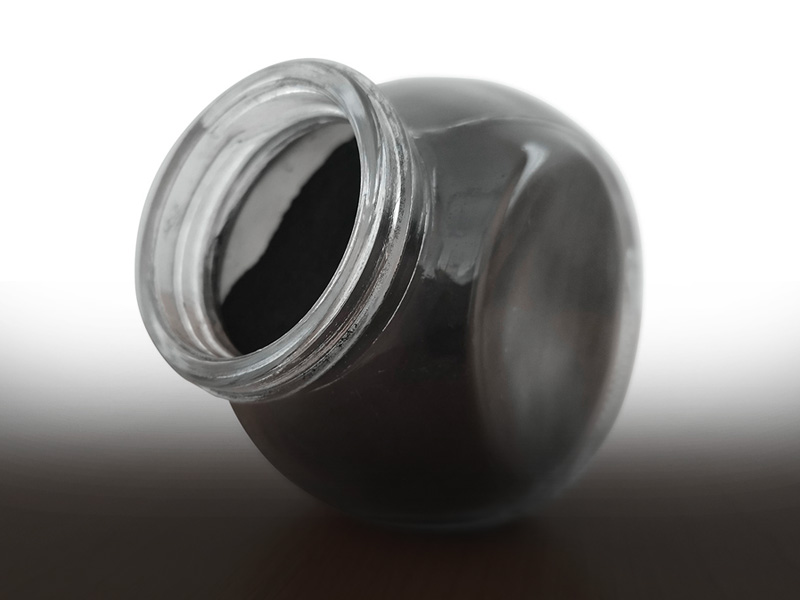

What is it designed for?
This fuel is used especially for shaft furnaces, rotary furnaces, lime furnaces, or carburizing furnaces. It is usable also in PCI (pulverized coal injection) technologies for blast furnaces as well as in non-energy sectors, such as in the chemical industry. It can find also another use in cast-forming mixtures.
Hard coal multipowders offered
Data sheets
Carbofuel 1
The quality of CF1 is characterized by more refined fraction than CF2, and mainly by higher SI (saturation index). This parameter is crucial for lime shaft furnaces, where it is unusable. That’s why this type of fuel is used in rotary furnaces both the lime and the cement ones. It is usable for the PCI (pulverized coal injection) technology in blast furnaces, as well as in the non-energy sectors like the chemical industry.
Our respected customers
Carbofuel 2
The quality of CF2 is characterized by slightly bigger fraction and the SI index (up to max. 1.5). This key parameter predestines this type of fuel for shaft lime furnaces. However, it’s also usable for rotary and PCI blast furnaces, depending on technology and customer requirements.
Our respected customers:
Foundry Carbon
This fuel is a patented mixture of hard coal and foundry additives. It is used as an additive to cast forming mixtures to increase the surface smoothness of the casted end products, and to remove them easier from the cast molds.